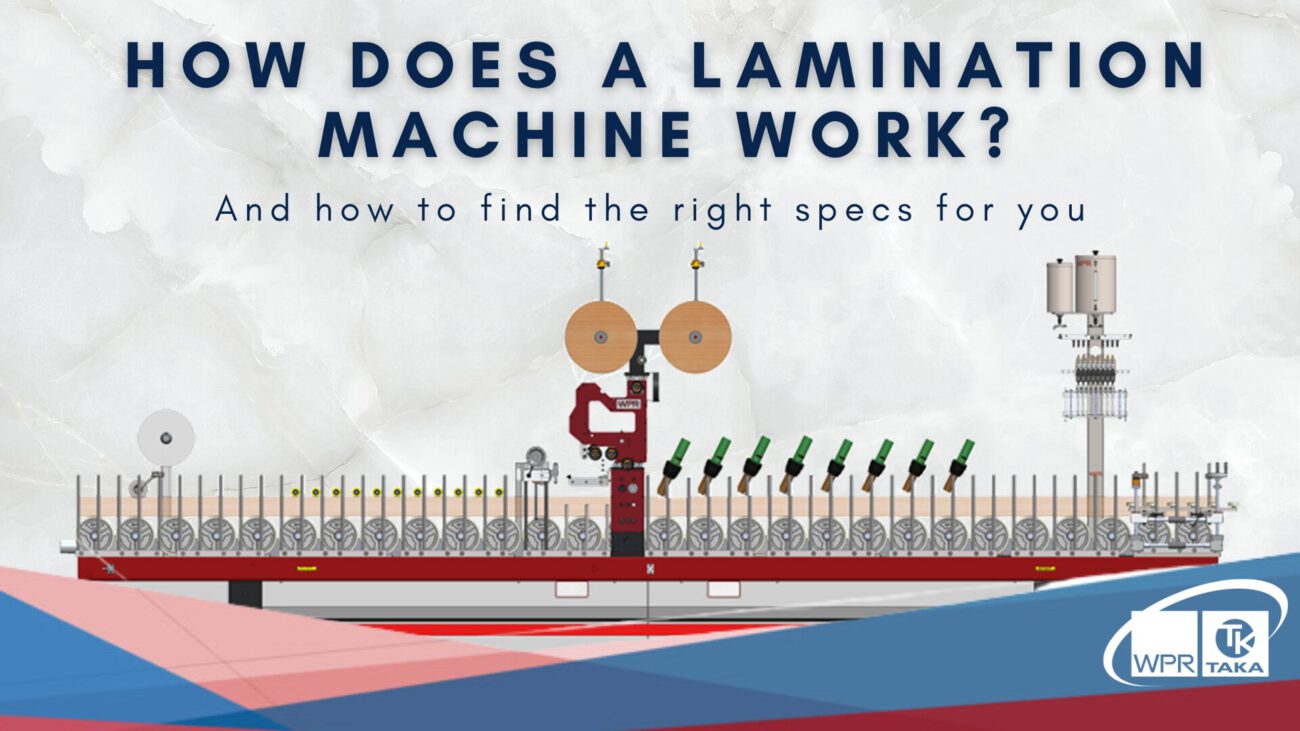
In the windows industry, profile wrapping is by far the most prominent surface colouring process. You can find this process also in other sectors like the furniture industry or flooring on different support materials like plastics, aluminium or wood. Thanks to a vast choice of colours and decors combined with a reliable and long-proven process that even enhances the longevity and resistance of the profiles, profile wrapping has become the most common process for the design of surfaces. But how does a wrapping machine work and what points do you need to pay attention to?
Bespoke technology
When you are at the point of choosing a profile wrapping machine for your production, be aware that there is no standard solution. Not if you are looking to improve and optimize your productivity.
Every situation and combination of materials must be considered for the right configuration of your machine. If you are looking for a quick return on investment the first point to start with is to sit down with the experts and specify your machine in every detail. With a clear idea of your goals and production needs, the machine manufacturer will translate your needs into the correct specifications, making sure that the machine will help to hit your targets from the first day.
Expected line speed, variety of profiles and colours, the adhesive primer system, and desired grade of automation are just a few of the essential points to take into account. Whoever goes for an off-the-shelf product will most probably experience the proverbial bitterness of a bad choice that remains long after the sweetness of low price is forgotten.
Process steps
Even though the basic function of a profile lamination machine is to bond a decorative foil onto a PVC or aluminium profile, there is a series of consecutive process steps that must be run through properly to obtain long-lasting foiling results.
Step 1 – Infeed and primer application
The incoming profile must be clean and fully pre-heated to a specific temperature. If this is not the case, the machine has to be equipped with cleaning and heating devices that create the ideal conditions. In the case of PVC and coated aluminium, an adhesion enhancer, a so-called primer, is applied on the surface to prepare the surface for the bonding. Different types of primers require different quantities and conditions. In any case, the primer needs to be spread homogeneously over the whole surface. Ideally, this happens by felt pads, because they have a double function of removing impurities and residues from the extrusion process while releasing the right amount of primer onto the surface.
Step 2 – Primer drying area
It is crucial to completely dry off the primer before the decorative foil touches the profile. Based on the type of primer and the line speed, the primer drying area has to be specified expertly and equipped with the right amount of air heaters. Otherwise, problems will occur as bubbles under the foil or complete delamination in the worst case. But if you follow the recommended parameters, this step will not create any issues. At the end of the primer drying area, the profiles are pre-heated again for the application of the decorative foil.
Step 3 – Glue application
Every foiling line is equipped with a hot melter, a glue melting device for the hot melt polyurethane adhesive. The glue is then pumped through a heated hose to the glue head, the slot nozzle, which spreads the melted glue onto the passing decorative foil. It is essential to follow the recommended quantity of glue and only work with a perfectly clean slot nozzle to achieve a perfect glue line. Any impurities might lead to stripes or dots under the decorative foil and consequently to claims.
Step 4 – Foiling area
The central point of a lamination machine is the application of the foil on the profile. A nip roller presses the foil with the glue on its backside onto the primed surface of the profile. At this point it is necessary to guarantee the correct temperature of the profile and the foil to obtain a successful bonding. The following series of smaller rollers press the foil onto the shape of the profile. An eventual excess of the foil is trimmed off and the foiled profile runs out of the machine just to repeat the whole procedure continuously with all bars that run through the machine.
Expertise is the key to quality
There are many technical solutions to optimize the set-up times and production capacities of a machine. The most advanced machines even feature an automatic setup. The latest generation of foiling machines has an automatic process control that monitors all relevant process parameters, regulates the heating devices, and reads out the production data into an ERP. Still, the knowledge and expertise of the operators on the machine cannot be fully replaced and are the decisive elements that decide over good or poor quality.
Therefore, make sure to train your staff regularly on the foiling process so they will spot and fix any quality issues before the quality control lab will. This is where real process optimization starts and how quality can be guaranteed continuously.
Where to find that knowledge?
If you do not have that knowledge or experience in your company, find a reliable partner that provides the technology AND the relevant know-how to set free the synergetic effects of an equal partnership. Challenge us and contact at our Contact section