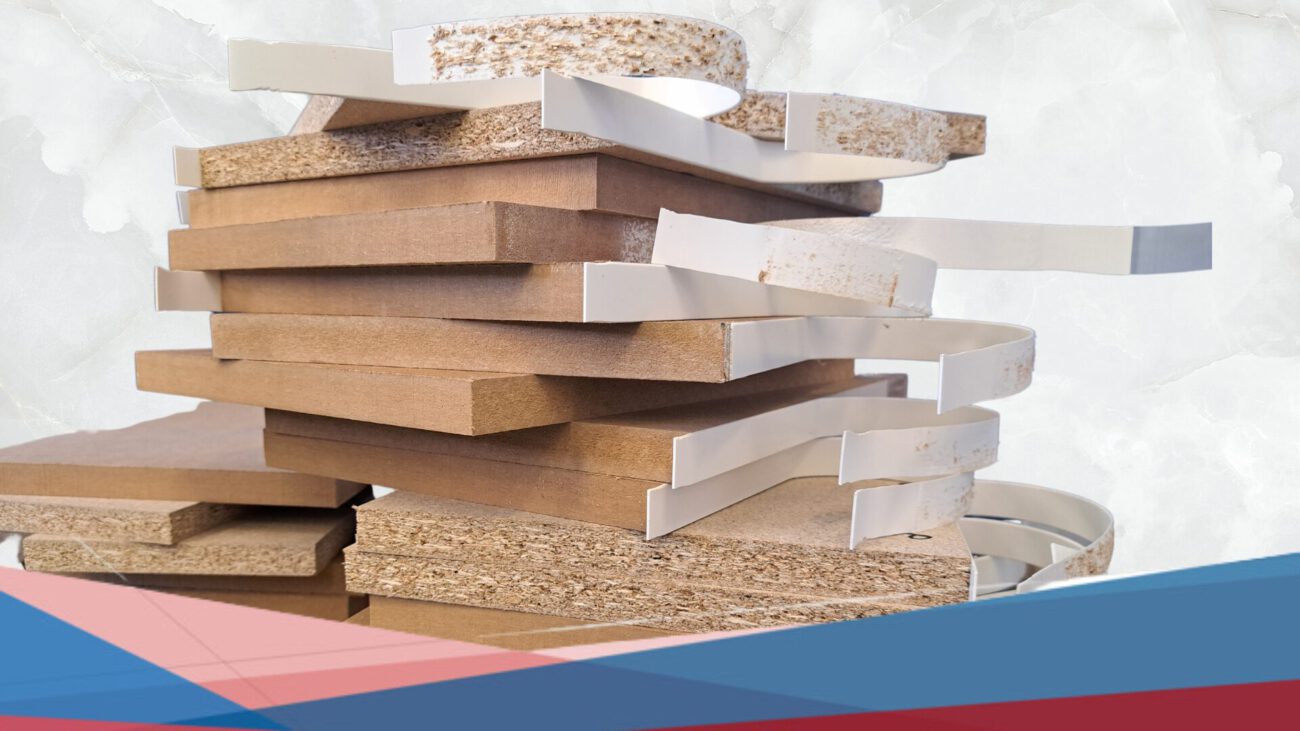
Edge bonding or edgebanding is the final part, yet a decisive step, of the production process of panels, doors and other furniture elements once the surface finish has been applied.
In fact, after the flat surface has been laminated or painted, the sides of the panels must be modified to match the chosen colouring and surface finish but also to protect the panel against infiltration from water or vapours.
Usually, the edges are glued to the panels by means of hot melt adhesives to create an almost invisible and perfect adhesive joint between the edgeband and the panel.
A vast choice of edges on the market
The edges are usually long and thin strips that can be made of plastic materials like PVC, PP, ABS, melamine or even veneer and aluminium and are supplied in big coils. They are available in any imaginable colour with infinite surface options in order to create always more appealing and innovative products.
The growing demands of customers include resistance to wear and tear and knocks on furniture and doors. Therefore, edgebands with material thicknesses of up to 3mm are used to protect the panel edges. For this reason, the adhesive used in processing must have outstanding initial adhesion to counteract the material memory of the stiff edgebands and to bond them successfully and permanently to the supporting material.
Different applications of edgebanding
The edge bonding technology depends on the morphology of the supporting materials. Edgebands can be applied on linear and square shaped panels but also on curved shapes and moulded edges, also known as soft forming An edgebanding machine spreads the glue on the edge of the supporting material, the edgebands are pressed onto the glue line subsequently by a series of pressing rollers. A particular edgebanding process is called postforming, in which the edgebands are applied prior to the lamination process in which the decorative foil is then applied also onto the closed edges.
A reliable process is the key
The variety of materials of panels, edges and adhesives lets manufacturers face an overwhelming complexity, which can easily lead to defects or unsatisfying results. . Therefore, it is key to establish a reliable and controlled production process to guarantee quality products on a constant high level.
The WPR-TAKA Academy is available for production audits and advice on how to optimize the production process and quality control. Do not hesitate to contact us in case you have any questions.