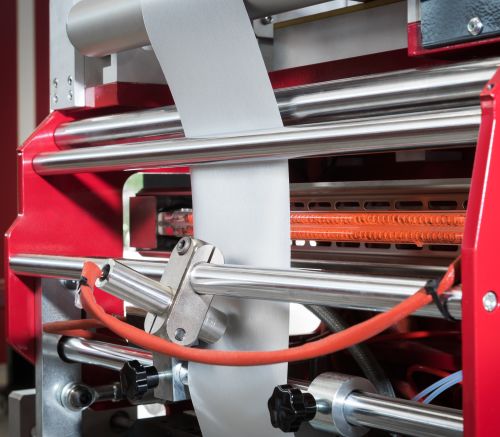
The glue application phase is one of the most critical phases in the lamination process, and to ensure that it is done correctly it is necessary to pay attention to the following features:
The HMPUR adhesive temperature inside the melting unit must remain between 100° and 140°C (according to the rate of consumption per hour). In order to guarantee a long life span for the adhesive, inert gas (nitrogen) or dehumidified air is used inside the melting units.
The glue coating head temperature should be between 130° and 140°C, and the quantity of adhesive for PVC and aluminium profile wrapping should be 40-60 g/m2. Usually, the melting units are set to the lowest temperature and the coating head to the highest, so as to enhance glue stability in the melting unit (without viscosity increase/reticulation).
It is important to check the quantity of glue spread on the foil on a regular basis, to be sure that it corresponds to the system settings.
Another important aspect to be taken into account is downtime, that is to say, when the system is stopped (for instance, to set up the profile change) for more than 30-50 minutes; in such cases, it is important to bring the system temperature down to 80°C to increase glue stability and keep the melting unit and the thermoregulated pipe clean.
In order to obtain a perfect coating, without lines, it is important that the coating head be kept clean and efficient, by cleaning and changing the filter regularly. After a pause, it is necessary to clean the coating head with a short glue shot (5-10 sec) to eliminate the adhesive that remained on the lip, and then to clean the lip with some rigid paper or brass brush (brass is the best material, as it is sufficiently hard but not so hard as to damage the coating lips).